What is EPDM?
EPDM is Ethylene Propylene Diene Monomer. It is an artificial rubber that is used in a variety of different applications. EPDM is most often utilized in the construction and automotive industries for seals of various kinds due to its outstanding resistance to environmental elements like UV, Ozone and weathering.
EPDM Applications
Typical applications of EPDM include window and door seals (glazing), sealing waterproof sheets, and electrical gaskets. It is worth noting that EPDM isn’t the ideal choice compared to its rival elastomer silicone rubber in terms of temperature resistance.
EPDM Temperature Range
Compared with silicone rubber, EPDM does not have the same resistance when heated to higher temperatures, as it can only be used at the maximum temperature of 130 degrees Celsius (266degF).
What is Silicone Rubber?
Silicone is an inorganic polymer composed of hydrogen, carbon, and oxygen (along with silicone). Silicone is widely used across numerous industries and applications, including transportation, aerospace, food/beverage and automobiles, among others.
Silicone rubber offers a variety of advantages. However, it is most well-known for and utilized due to its resistance to extreme temperatures. In contrast to EPDM, which is unstable, silicone remains solid and maintains its physical properties to 230degC (446degF) and higher temperatures. Silicone materials can stand up to 270degC. It is not just that silicone is ideal in extreme temperatures. Still, it’s also regarded as a sterile elastomer; that’s why you’ll be able to find it used in the beverage and food industry for milk tubings, seals, and gaskets for food machinery, as well as vending tubing in drink machines.
Silicone is regarded as the more durable elastomer over EPDM because of its additional advantages, having a longer service life, which means lower replacement costs and less downtime.
How is Silicone Manufactured?
Silicone can be manufactured in various ways based on the types of silicone being used. Silicone can come in three forms, namely LSR’s (liquid silicone rubbers) as well as RTV’s (Room Temperature Vulcanisation) and HTV’s (High-Temperature Vulcanisation).
Elastostar Rubber Corporation manufactures HTV silicone rubber. The silicone is formed into the exact shape needed before going through a heat curing process to create the final product. Silicones are produced in various kinds and shapes, such as sheets and rolls, tubes cords, profiles, and sections. They can be made in sponge or solid silicone based on the application(s).
Silicone vs. EPDM Technical Comparison
Temperature: – Resistance to temperature is essential in using applications with varying temperature ranges. Selecting the wrong rubber could cause deformation, melting, or the material becoming brittle, which will alter its physical properties, and more likely to cause failure. Compared to the silicone rubber, EPDM fared much worse, with the highest temperature being 130degC (266degF). It can maintain temperatures of 230degC (446degF) and even 270degC (518degF) for high-temperature silicone grades.
Elongation: – Elongation refers to the degree of stretchiness a material has and how it behaves when expanding and contracting. It is mainly dependent on Shore A hardness and is usually associated with solid rubbers compared to foams or sponges.
Silicone is seen as a more stretchy rubber than EPDM, which is why silicone is used as a vacuum membrane due to its high tear resistance and elongation of up to 800%. Vacuum membrane presses assist in creating and joining composites with each with extreme pressure. Silicone is also flexible to temperatures of -60°C, and this is why it’s utilized in extreme environments.
Oil Resistance: – Although both materials are prone to swelling if exposed to oil for long periods, silicone has better resistance to oil. It is seen as a more suitable material for the two, and silicone can be formulated to have additional resistance to oil for demanding applications.
Environmental Resistance: – If the rubber is going to be used in an application located within an outdoor setting, the resistance to environmental conditions of the rubber must be evaluated. Certain rubbers are vulnerable to cracks when exposed to Ozone and UV light; therefore, choosing the appropriate rubber for outdoor use is crucial. EPDM and silicone are extremely resistant in the face of environmental factors. Both rubbers can stand up to general weathering, UV and Ozone, making them suitable for outdoor use.
Tear Strength: – Tear strength/resistance refers to how resilient an item is to tear. EPDM has a high tear strength and is considered the most durable rubber compared to silicone. However, silicone is much more flexible and can be designed to offer a high degree of tears and lengthening. It is perfect for vacuum membranes.
Temperature Comparison
No matter how cold or hot, variable temperatures can have negative consequences on all rubbers. The heat in particular will alter a rubber’s mechanical properties, impacting the seal’s performance.
It is essential to be aware of a material’s resistance to temperature before putting it into an application to ensure that the time between failure and failure is minimized.
We’ve developed an indicator of temperature resistance Silicone and EPDM, which shows the limit of each at different temperatures.
Moving the slide bar around, you can observe the temperature limitations for each material. When the circles shrink, the rubber has reached its limit before being affected by temperature.
HOT | COLD |
+130°C EPDM starts to degrade. | At -40°C EPDM reaches a brittle point |
+230°C Silicone starts to degrade. | At -40°C EPDM reaches a brittle point |
It is clear that silicone’s superior resistance to the temperature at both cold and hot temperatures. For any use that exceeds 130de, silicone should be the best choice.
In colder temperatures, both materials work well, with silicone having an advantage due to its ability to withstand temperatures up to -60degC.
How Heat Affects Silicone vs. EPDM
As shown in the diagram, silicone rubber and EPDM vary when exposed to different degrees of heat.
Our Laboratory team carried out several tests of heat age using a standard silicone sponge and a regular EPDM sponge. Both had a thickness of 6mm.
Six circles measuring 58mm were cut out of the original pieces and placed in the oven for a few hours at various temperatures. The outcomes were then documented in the following manner:
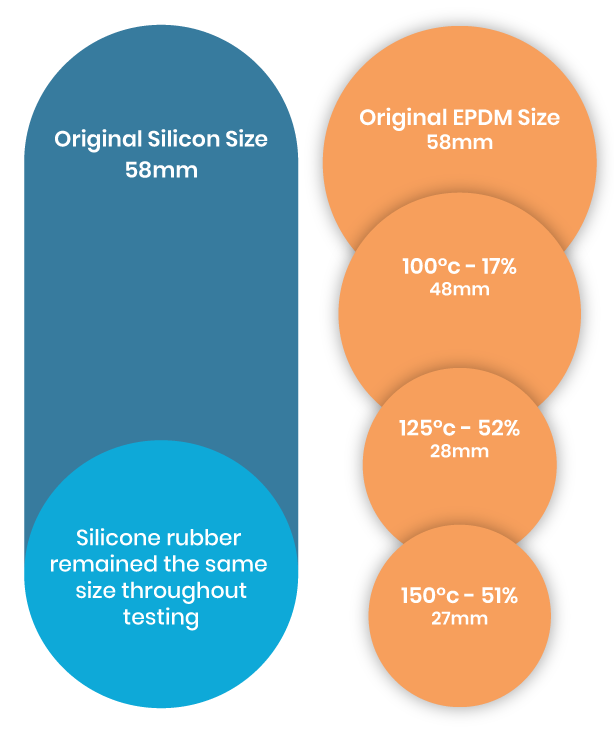
EPDM Results
At 100°C, the EPDM sample had shrunk by 17% to 48mm. A surprising result considering that the datasheet indicated the temperature limit was 130°C.
At 125°C the shrinkage continued, but it was more severe, showing a 52% decrease from its original size to 28mm.
Finally, at 150°C the EPDM had decreased but only by a further 1mm, concluding that 125°C is where the material saw severe deformity.
Silicone Results
The silicone samples did not show any shrinkage when exposed to the same temperature as EPDM. The silicone rubber samples all remained at 58mm after being taken out from the oven, demonstrating the strength of silicone when heated to high temperatures.
Why Choosing the Right Material is Important?
The reason for application failure is often due to human error, regardless of whether during the design or the installation phase. Based on the application you are using, selecting the appropriate material will determine the effectiveness or failure of the application.
Many sealing failures occur due to the incorrect rubber being chosen, sometimes due to price, lack of knowledge on the application environment, or both.
At Elastostar Rubber Corporation, we first gain thorough knowledge from our clients about the location they intend to place the rubber and what conditions it might encounter. Abrasion, temperature, chemical contact, and pressure are all essential factors to consider when deciding on silicone rubber instead of EPDM. Our specialist team of engineers and silicone experts are on hand to advise and help you understand the advantages of silicone over EPDM and how using silicone in an application will give better lifespan and longevity, keeping downtime to a minimum.
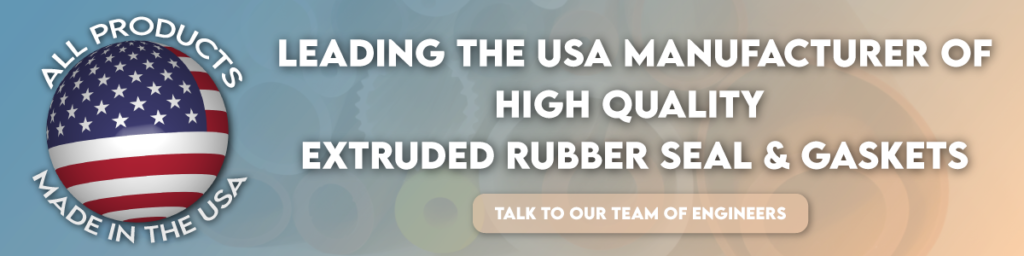
Elastostar is proud to offer the highest quality components and rubber parts in the industry. We have been a trusted manufacturer of custom and standard size extruded rubber seal and gaskets parts for the food equipment, medical, pharmaceutical, industries, Glass, window& door industries.
Our advanced facilities and experienced experts can create FDA medical-, medical and surgical-grade tubing and other top-quality products. All the products are made of various rubber-based materials, including silicon rubber. To find out more about our top Silicone Rubber products and solutions, please get in touch with us now or request a quote today or call us on +1 614-841-4400.
Ask the Experts
Got a Question? Ask an Elastostar Rubber Corporation today.
Our silicone elastomer experts will provide answers to your questions.