What Is A Die Cutting Gasket?
As the term ‘gasket’ suggests, a die cutting gasket is meant for industrial purposes.
Let’s focus on the definition of die-cutting gaskets and know what it is.
Die cutting gasket basically plays the role of a seal in between two surfaces that are different from each other. When the bolt load is just enough, it creates a compressive force. Compressive force is the force that occurs when another physical force pushes an object inward so much that it results in the object to be compressed or compacted. This compression can last temporarily or permanently, depending on the type of material the force is being exerted on. There may be different results due to the amount and type of force exerted and the direction towards which the force is exerted.
This is where a die cutting gasket comes in use. The die cutting gasket seals the gap left between the two different surfaces. This gasket also possesses the characteristic of filling up the imperfections or flaws in the mating surfaces. This stands to act as an advantage since it helps in solving or erasing existing and potential defects and application errors.
What Are The Applications Of Die Cutting Gaskets?
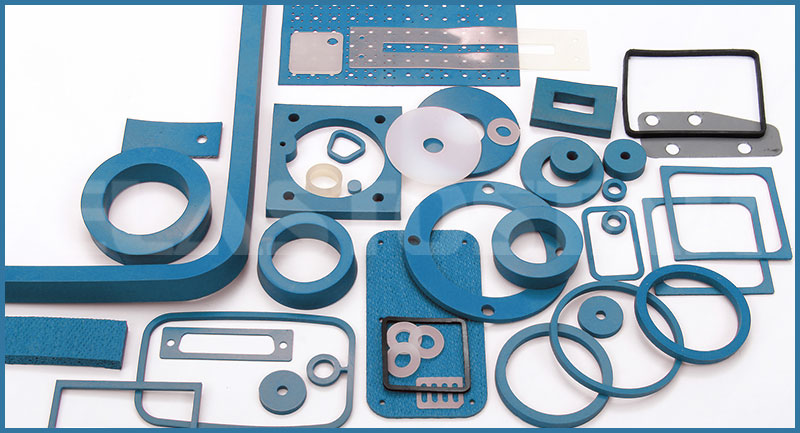
As already mentioned, these die cutting gaskets are meant for industrial purposes. Few of them are listed down below:
- Plumbing
- Medical instruments
- OEM (Original Equipment Manufacturers)
- Commercial purposes and applications
- Aerospace industry
- Automotive
- Agricultural purposes including irrigation
- Electrical purposes involving lighting, electronics, etc
- Controls and other gadgets like valves, bearings and pumps
Now, since we have already discussed briefly the definition and applications of die cutting gasket, let us talk about the characteristics of die cutting gaskets.
Characteristics Or Traits Of Die Cutting Gaskets:
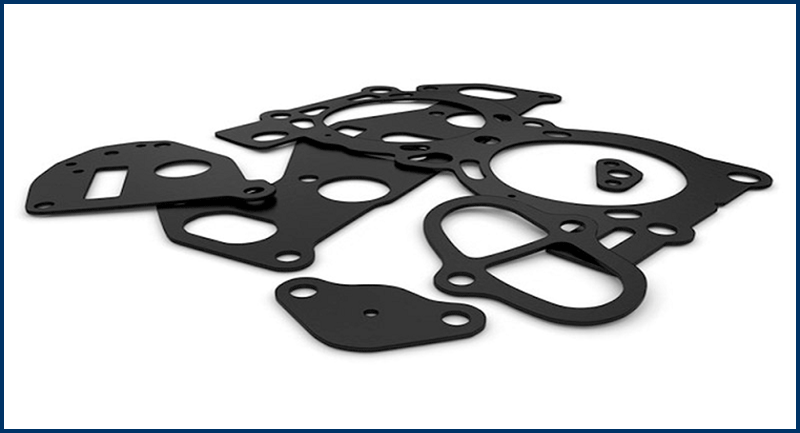
There are indeed several characteristics of die-cutting gaskets. The important ones are mentioned down below-
1.) Low Cost:
Die-cutting gaskets are essentially cheap and thus have the future of being cost-efficient. This is indeed a very useful and important trait or feature since calculated cost and expenditure is an essential aspect for every company. Thus, die cutting caskets come with the advantage of not making a hole in the company’s capital.
2.) Low Set-Up Cost::
Die-cutting gaskets are very cheap and easy to set up or mount. It is most definitely not rocket science! The materials that are used in these gaskets are manufactured with such materials or are used in such instruments that help to reduce costs. The type of gasket chosen helps in reducing the cost of the entire project as well. Steel rule die is the least expensive die gasket of all. Steel rule dies are preferable for low volume productions, especially when the die is required in a very short amount of time span. The cost of setting it up is not very expensive. As already mentioned, cost-effective instruments and processes are very beneficial for any company.
3.) The Supply Chain Of Die Cutting Gasket Is Really Flexible::
Die-cutting is really a global industry. These industries are quite widespread. Customers have the advantage of choosing their die-cutting source from several other companies. They can choose companies that are near them or they can choose firms or industries that operate in other countries. However, shorter supply chains are known to reduce cost up to an essential height compared to longer supply chains. A shorter supply chain means a supply chain that is generated from any firm or company that is near the purchaser or customer. The long supply chain implies a supply chain that is generated from a company or firm that is located geographically far from the customer. There is the widespread availability of die-cutting gaskets. This is definitely an advantage for customers and newly operating firms. The materials of these die-cutting gaskets obviously differ from firm to firm. Due to its flexible supply chain, customers can choose the gasket that best suits the need of the customer or the instrument it is required for.
4.) Designs Of The Die Cutting Gasket Can Be Changed Without Excessive Tooling Expenses:
Only digital die cutting are the ones that don’t require tooling at all. Except that, all die-cutting gaskets require tooling. However, the tooling of metal dies cutting gaskets does not necessarily have to be expensive. Smart designs and alterations are required to be made but this has to be kept in mind that the expenses or cost does not go overboard or extend and reach a limit that a customer and company cannot afford or bear to have.
5.) Die Cuts Are Preferable
Die cuts are immensely preferred if a customer or company requires cuts of different shapes. Though die-cutting can be a bit costlier than lathe cut gaskets, the former can be made to fit different instruments as they possess the characteristic of being formed to fit considered and specific instruments and applications.
6.) Rapid Production Method:
Another very important and immensely useful advantage or quality of die-cutting gaskets. These cutting gaskets offer short and quick turnaround time with the precision die-cutting process. The precision die-cutting process is considered and known to be the fastest production method for gaskets and seals, nowadays. In today’s days, speed is everything! Precision die-cutting is just what is required to avoid inconvenience when within a very limited timeline. One does not have to wait for long for a gasket or seal to be replaced or changed or altered. If time is a major factor for the fitting or production of any instrument then precision die-cut gaskets are definitely the ones that might just save the day!
7.) Versatile:
One of the most difficult yet significant aspects of these types of gaskets is to find the perfect match to be mounted on an instrument and satisfy the exact requirements of any application. Well, die-cut gaskets are just what is needed to mount and actually perfectly fit the instrument or machine and provide optimum efficiency.
For more use and application, please contact us with your details or Email us on info@elastostar.com or Call us on 614-841-4400. We will help you to explore more ways to utilize our products for your special purpose.